Cold Foil Printing
In the ever-evolving world of printing technology, numerous innovative techniques have emerged to enhance the visual appeal and aesthetic value of printed materials. One such technique gaining popularity is cold foil printing.
Cold foil printing is a modern printing process that adds a metallic, reflective finish to various substrates, ranging from paper and cardboard to synthetic materials. Unlike traditional hot foil stamping, which uses heat to transfer foil onto the surface, cold foil printing utilizes adhesive and UV curing technology to achieve stunning metallic effects.
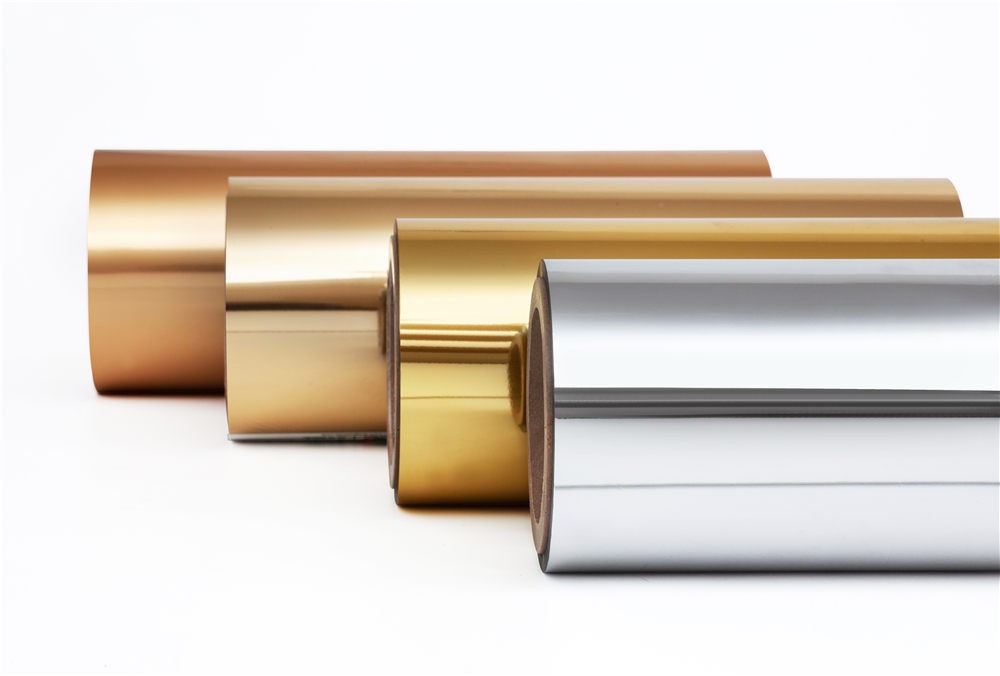
The cold foil printing process involves several stages, each contributing to the creation of eye-catching designs.
The process begins with the preparation of the artwork or design to be printed. Special consideration is given to areas where the cold foil will be applied, ensuring they are properly defined in the design files.
The substrate, typically paper or cardboard, is first printed using conventional printing techniques such as offset or flexography. The desired design is applied using standard inks, forming the base layer.
After the initial printing, an adhesive is applied to specific areas where the cold foil will be bonded. The adhesive is carefully registered to match the desired foil placement accurately.
A roll of metallic foil is unwound, and it passes through a series of rollers. As it passes through the nip rollers, the adhesive-coated areas come into contact with the cold foil, which adheres to the substrate through the pressure exerted by the rollers. Only the adhesive areas receive the metallic effect, while the non-adhesive areas retain the base layer color.
To solidify the bond between the cold foil and the substrate, the printed material is passed through a UV curing unit. The UV light rapidly cures the adhesive, ensuring a strong and durable metallic finish.
Cold foil printing offers numerous advantages, making it a preferred choice for designers and printers alike. Some notable benefits include:
Cold foil can be applied to various substrates, including paper, cardboard, and synthetic materials, allowing for creative freedom and endless design possibilities.
Compared to hot foil stamping, cold foil printing requires less setup time and eliminates the need for expensive metal dies, resulting in cost savings.
Cold foil printing can be integrated into existing printing processes, such as offset or flexography, enabling efficient and seamless production.
The ability to register the foil precisely offers designers the freedom to incorporate intricate details, textures, and multi-colored foils into their designs.
Cold foil printing produces minimal waste, as only the areas requiring foil are coated, reducing material consumption and environmental impact.
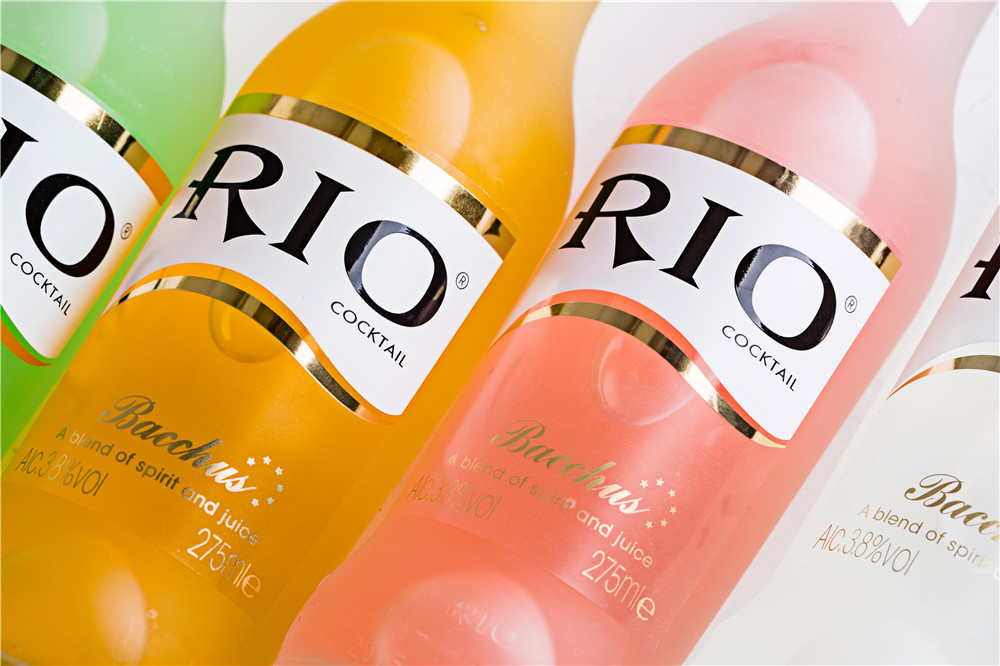
Cold foil printing changed the printing industry by offering a cost-effective, versatile, and visually stunning method to add metallic finishes to printed materials.
With its seamless integration into existing printing processes and limitless design possibilities, cold foil printing has become a go-to technique for elevating the appeal of packaging, labels, marketing collateral, and other printed materials.
As the demand for eye-catching and captivating designs continues to grow, cold foil printing remains at the forefront, adding a touch of brilliance to the world of printing. As technology continues to advance, we can expect further innovations in cold foil printing, unlocking even more creative possibilities and raising the bar for printed materials' visual appeal.
What is Cold Foil Printing?
Cold foil printing is a modern printing process that adds a metallic, reflective finish to various substrates, ranging from paper and cardboard to synthetic materials. Unlike traditional hot foil stamping, which uses heat to transfer foil onto the surface, cold foil printing utilizes adhesive and UV curing technology to achieve stunning metallic effects.
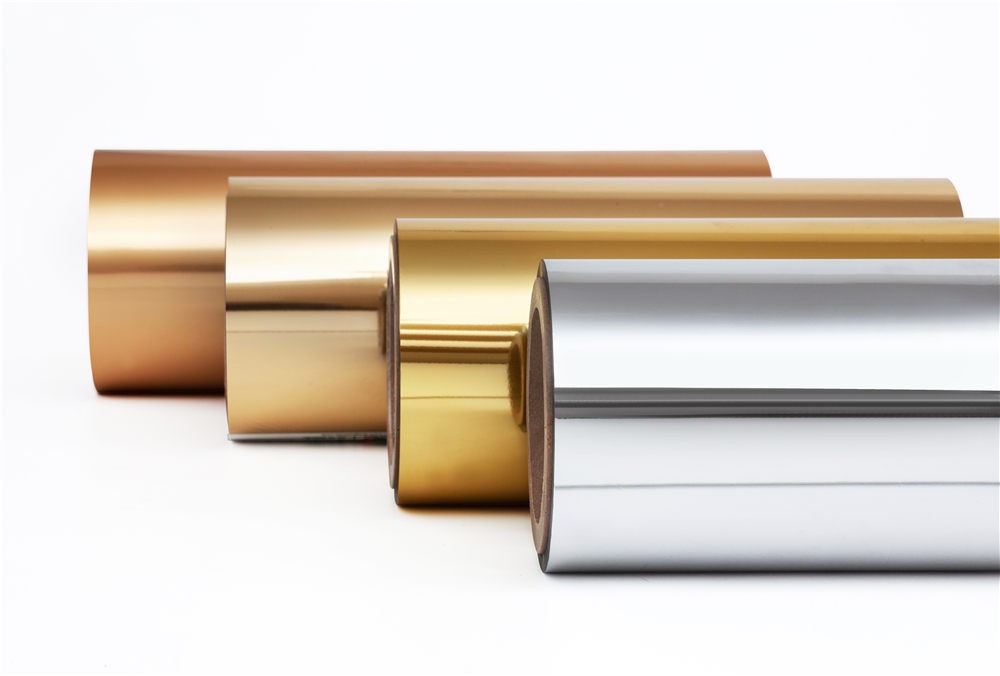
Cold Foil Printing Process
The cold foil printing process involves several stages, each contributing to the creation of eye-catching designs.
● Prepress
The process begins with the preparation of the artwork or design to be printed. Special consideration is given to areas where the cold foil will be applied, ensuring they are properly defined in the design files.
● Printing
The substrate, typically paper or cardboard, is first printed using conventional printing techniques such as offset or flexography. The desired design is applied using standard inks, forming the base layer.
● Application of Adhesive
After the initial printing, an adhesive is applied to specific areas where the cold foil will be bonded. The adhesive is carefully registered to match the desired foil placement accurately.
● Cold Foil Transfer
A roll of metallic foil is unwound, and it passes through a series of rollers. As it passes through the nip rollers, the adhesive-coated areas come into contact with the cold foil, which adheres to the substrate through the pressure exerted by the rollers. Only the adhesive areas receive the metallic effect, while the non-adhesive areas retain the base layer color.
● UV Curing
To solidify the bond between the cold foil and the substrate, the printed material is passed through a UV curing unit. The UV light rapidly cures the adhesive, ensuring a strong and durable metallic finish.
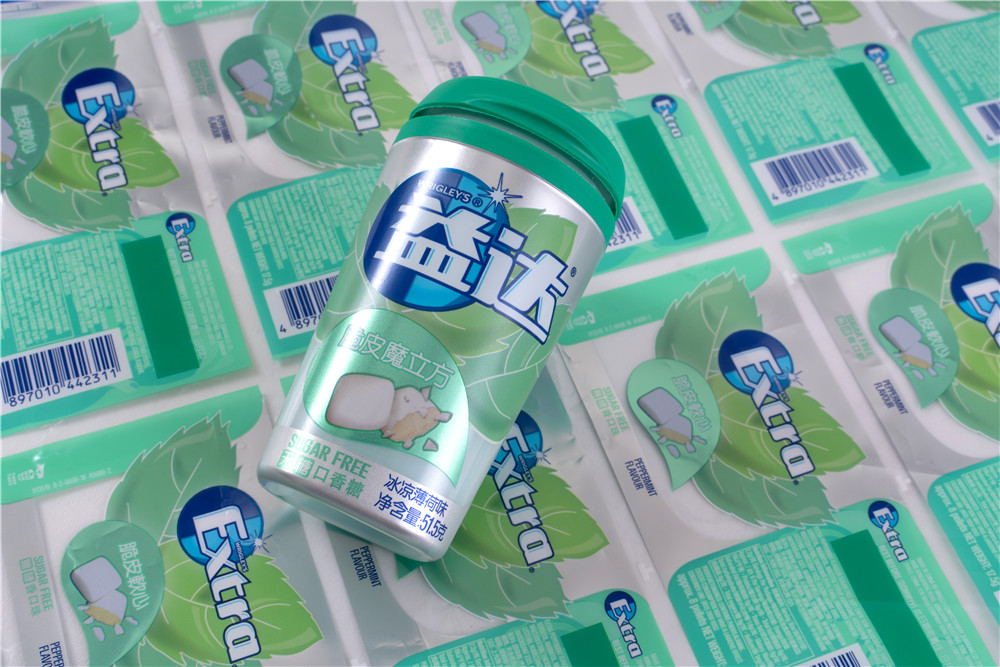
Advantages of Cold Foil Printing
Cold foil printing offers numerous advantages, making it a preferred choice for designers and printers alike. Some notable benefits include:
● Versatility
Cold foil can be applied to various substrates, including paper, cardboard, and synthetic materials, allowing for creative freedom and endless design possibilities.
● Cost-effectiveness
Compared to hot foil stamping, cold foil printing requires less setup time and eliminates the need for expensive metal dies, resulting in cost savings.
● Inline Application
Cold foil printing can be integrated into existing printing processes, such as offset or flexography, enabling efficient and seamless production.
● Enhanced Design Flexibility
The ability to register the foil precisely offers designers the freedom to incorporate intricate details, textures, and multi-colored foils into their designs.
● Environmentally Friendly
Cold foil printing produces minimal waste, as only the areas requiring foil are coated, reducing material consumption and environmental impact.
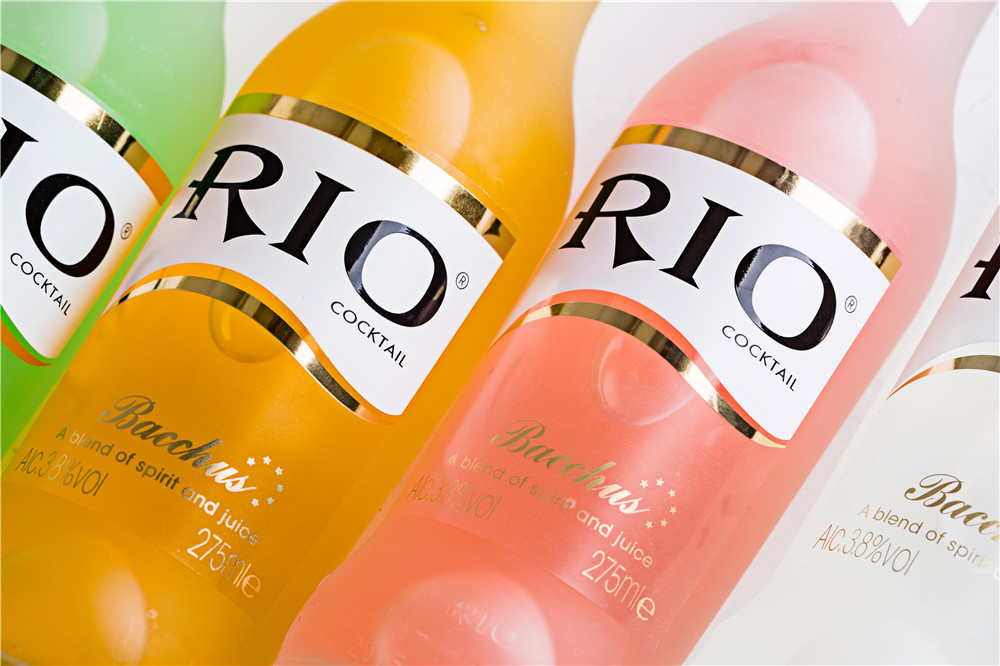
Cold foil printing changed the printing industry by offering a cost-effective, versatile, and visually stunning method to add metallic finishes to printed materials.
With its seamless integration into existing printing processes and limitless design possibilities, cold foil printing has become a go-to technique for elevating the appeal of packaging, labels, marketing collateral, and other printed materials.
As the demand for eye-catching and captivating designs continues to grow, cold foil printing remains at the forefront, adding a touch of brilliance to the world of printing. As technology continues to advance, we can expect further innovations in cold foil printing, unlocking even more creative possibilities and raising the bar for printed materials' visual appeal.